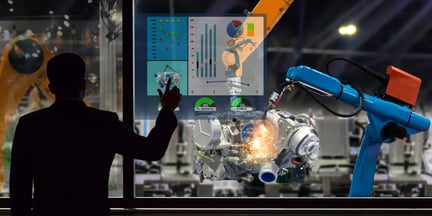
Industry 4.0 and digital transformation: what are today’s critical issues?
The digital transformation of heavy industry and manufacturing companies is a real development opportunity for the manufacturing sector and Québec’s economic growth. As in the case of any transformation, this comes with its share of issues and challenges. In a changing world where many operations are performed remotely, and even by telework, it is essential to put data at the core of your digital transformation strategy.
For less than a decade, the Internet of Things, Industry 4.0 and digital transformation have shaken companies and generated radical changes, not only to systems and processes, but also to management styles, business models and the workforce. Rapid technological change, the transformation of trades and customers’ new requirements today are pushing industries to remodel their plants to become more innovative, more competitive and job creating.
This transformation is essentially defined by the integration of new technologies into the corporate value chain. Massive use and management of data (Big Data), interconnection machines (Industrial Internet of Things – IIOT), automation and robotization will allow more flexible and customized production for the future.
In fact, the needs are unique to each company and it is preferable to be realistic about your ambitions, because the deployment of a digital strategy integrated into the corporate strategy, including the acquisition of new technologies, represents several issues for managers.
Initially, by targeting small transformation objectives, this will make it possible to obtain faster productivity gains, often with a minimum investment. Here are some of the critical issues where Norda Stelo can support you:
1. Improving productivity by enhancing data
The adoption of digital technologies provides a long list of advantages, including a substantial increase in productivity, turnover, product quality and overall customer satisfaction.
According to a recent survey by Business Development Bank of Canada, conducted among approximately 1,000 entrepreneurs, 60% of adopters affirm that digital technologies have contributed to increase their productivity substantially. Moreover, 50% of adopters affirm this helped them reduce their operating costs and 42% say they improved the quality of their products.
First of all, the places must be identified where more data must be acquired to conduct the analysis, and then the necessary adjustments can be prioritized. In this manner, productivity can often be optimized quickly, with only small investments.
The real-time data will provide the necessary agility to make informed choices in order to anticipate and prevent unwanted production stoppages, optimize production efficiency and improve equipment maintenance.
Real-time data collection for a production line will give us the ability to adapt to changes that may be caused by a breakdown, an abnormal reaction of the process or a faulty operation. This adaptability to change is the spearhead of the Industry 4.0 revolution.
2. Maintenance and asset management
Considered the Holy Grail of digital transformation, predictive maintenance has become the ultimate quest to detect failures in time and avoid costly unscheduled production stoppages.
With the installation and programming of sensors and measuring instrumentation, equipment readings are taken easily according to the actual conditions of use. The analysis of the data coming from the monitoring systems thus makes it possible to determine the probability factors of a failure and intervene rapidly.
Another way to reduce the costs and impacts of equipment maintenance is to automate and robotize the maintenance tasks in order to obtain shorter production shutdowns and avoid the issues related to workers’ safety, such as work in confined spaces, work at heights or risky environments.
Moreover, in line with the Industry 4.0 revolution, Norda Stelo’s Asset Integrity and Reliability Centre of Excellence has developed a new collaborative platform for asset management and maintenance, intended for any type of tank farm. This new tool combines the power of smart technologies and depends on the cutting-edge expertise Norda Stelo has possessed for several years in asset integrity and reliability management. For more details on our collaborative asset management platform, go to: https://collectiveingenuity.norda.com/tank-farm-health-review
Moreover, in a perspective of partnership with our customers, our expert maintenance team is working on the development of new tools that will allow guidance of maintenance operations in the plants. We are currently developing a tool using augmented reality to facilitate maintenance of specialized equipment and machines.
3. Machine safety
Today, more than ever, health and safety management in the plant is a primary concern and must be an integral part of the Industry 4.0 process. With the Industry 4.0 revolution, the OHS approach to secure machines will be integrated, accounting for a multitude of data that will allow real-time access to all information relating to operating status, for example, thus facilitating preventive interventions on the machines at risk.
Because all the machine data can be compiled on a computer platform, it becomes easier to analyze the impacts, take corrective actions and produce the detailed report for each machine. For example, for standalone machines, the information collected can serve to bypass and avoid locations or positions that put workers’ health and safety at greater risk.
On the strength of expertise in plants during operation, Norda Stelo supports the deployment of Industry 4.0 strategies with the goal of ensuring a smooth transition to these new technologies. Our enviable expertise in the fields of instrumentation-control, robotics, industrial IT and telecommunications is applied regularly to meet the needs and technological challenges present in the manufacturing industries and heavy industry. Making the move to Industry 4.0 with Norda Stelo means counting on a seasoned team, driven by new technologies and supported by solid experience.
Back to blog