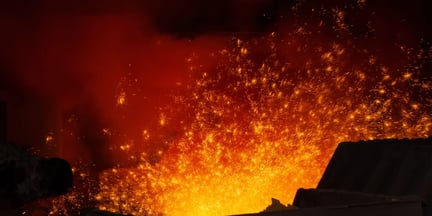
High Temperature Process Equipment Decarbonization
In the collective effort to decarbonize our industries, certain sectors face greater challenges in this endeavor. Such “hard-to-abate” sectors are industries characterized by process-related carbon emissions and other hazardous air pollutants, with limited straightforward options for significant emission reductions.
These sectors namely involve the transformation of raw materials in high-temperature environments through kilns, furnaces, calciners, or smelters.
Decarbonizing high-temperature process equipment is a significant challenge within these industries. Applying a sound understanding of the reliability and productivity of process assets can help to accelerate the decarbonization of these facilities. This article provides insights into the range of abatement pathways, their potential, and their challenges.
While decarbonization of high-temperature process equipment is evolving, the following offers early, high-level insights into the range of abatement pathways, their promise, and their challenges.
Processes and Pathway Options
To understand the decarbonization pathways, it is essential to review key industries and their processes, along with perspectives on the most viable pathways and why. While none of the processes below are identical to each other, it is important to appreciate their similarities as this creates learning opportunities within, and across sectors. The focus is on emissions from high-temperature process equipment, considering that:
- Electrified processes should source green power.
- Other distributed on-site emissions will exist.
- Deep energy efficiency should always be prioritized.
The pathways discussed do not include new, novel processes specific to certain industries, such as Elysis for aluminum production or Electra’s low-temperature iron plate production.
Copper & Nickel
Both copper and nickel are not only sometimes found in the same ore deposits they are processed similarly and often use the same equipment. Either can come in the form of two different deposit types in Canada, though typically in a sulphide and iron-rich host ore body. What makes this interesting from a GHG perspective is that O₂ can react with the sulphide minerals to generate heat as part of the process. A highly simplified way to think about copper or nickel sulphide processing is:
After the initial physical separation process (crushing/grinding, flotation), these sulphide metals could either be leached creating sulphuric acid or elemental sulphur that must be managed, or more commonly, flash smelted at over 1,200°C. In smelting, this is where oxygen is introduced to remove the sulphur and any iron where the concentrate reacts to form sulphur dioxide gas and an iron-silicate slag layer which are removed. The resulting matte (50-70% copper or nickel) is further processed again either through leaching with hydrogen as a reductant producing ammonia sulphate or put through a converter furnace where oxygen is injected to oxidize remaining sulphur and iron. This produces a 96-99% pure metal, which is then further refined again hydrometallurgically (sulphuric or ammonia acid leach) or through pyrometallurgy in an electrolytic refining process resulting in 99.99% pure copper or nickel. While the refining process is electrically driven, the heat for smelting and converting comes from the combination of a fuel and oxygen contributing to direct CO₂ emissions.
Aluminum
The aluminum production process involves an initial four stages: digestion, clarification, precipitation, and calcination. Alumina is generated from the calcination process which then goes through a final electrolytic reduction at a separate facility:
The bauxite is digested in an autoclave, heated by low-grade steam (240°C) with the addition of sodium hydroxide where it is then clarified, precipitated, and calcined at up to 1100°C in a final “popcorn” heating step. The alumina is then reduced to pure aluminum metal through electrolysis in aluminum “pots” where oxygen reacts with the carbon anodes, forming carbon dioxide. While this CO₂ is released in pure form from the anodes, it is combined with air ingress to generate a low CO₂ concentration flue gas. Casting, as a final step, will require both pre-heating of the aluminum to remove water and a furnace to cast aluminum logs, typically fired by natural gas.
Iron & Steel
Today, iron ore is incrementally heated to 1320°C in an induration furnace to generate pellets that are then transformed into steel most commonly through an integrated steel mill with a blast furnace and basic oxygen furnace process. A blast furnace is a tall, cylindrical structure lined with refractory bricks that can withstand high temperatures along with a cooling element (stave). It converts iron ore into pig iron and molten slag, an intermediate product with high carbon content where iron ore, coke, and limestone are layered (charged) into the blast furnace and with hot air blown (“blasted”) into the furnace igniting coke at high temperatures (~2,000°C). Coke then reduces iron oxides where the molten slag and pig iron are batch tapped. Limestone reacts with impurities (e.g., silica) to form slag, which floats on the molten iron. The pig iron product of a blast furnace is then followed by a Basic Oxygen Furnace (BOF) with pure oxygen blown into the molten metal, reducing carbon and impurities to produce a final steel product.
Growth in steelmaking, however, will be through the direct reduction of iron (DRI) process which produces a sponge iron that, while historically using coal or coke as an efficient reductant, is increasingly using gas with a significant focus on 100% H₂ as the reductant. Gas-based DRI is typically through a shaft furnace at ~800–1,100°C, though a fluidized bed option is quickly emerging that operates at lower temperatures. A DRI sponge iron product is either sent directly to an adjacent Electric Arc Furnace (EAF), often with scrap steel, or shipped as a hot briquetted iron (HBI) to an EAF or blast furnace. If iron ore in a DRI is lower quality (<65% iron), the DRI will first need to be melted to avoid high amounts of slag.
Note: CO₂ emissions are generated through both the chemical reactions of a carbon-based reductant and through the supply of heat, but the amount and proportion will depend on the reductant and fuel types used.
Lime & Cement
Cement and lime kilns are long, slowly rotating industrial refractory furnaces used for processing raw materials into clinker (cement production) or lime (lime production). While their principles of operation are similar, they differ in terms of feedstock, reactions, and final products.
Lime kilns produce quicklime (CaO) by decarbonizing limestone, where the limestone is heated to 900-1,000°C, decomposing into quicklime and releasing CO₂. Unlike cement kilns, lime kilns stop at calcination without forming complex compounds. The kiln is typically either a rotating cylinder similar to a cement kiln or a vertical static shaft kiln where limestone descends countercurrent to hot gases.
Cement kilns, on the other hand, produce clinker, the intermediate product in cement manufacturing. A mixture of limestone, clay, silica, and iron oxide are combined as the feedstock where the products are dried and preheated in a preheater tower or calciner using waste heat from the kiln. This “raw meal” is then calcined at around 900°C where the limestone decomposes into lime, releasing CO₂, where the lime then reacts with other components at 1,450°C to form clinker minerals. A range of fuel types are used currently such as coal and natural gas, increasingly supplemented by alternative fuels such as end-of-life tires or biogenic waste such woody biomass or even abattoir waste.
Reflections
Technically promising yet economically challenging pathways exist for all processes, with some more applicable than others depending on the process and local context. Significant capital and operating cost outlays will be required. CO2 capture and/or oxy firing, along with hydrogen, are consistent pathways available across all options. Collaboration at scale is essential to decarbonize high-temperature processes effectively. Any solution should have its full life-cycle emissions quantified to understand the overall net reductions.
Note: This article acknowledges that there may be other pathways and differing perspectives not covered. It also recognizes the limitations and context in explanations due to the article's brevity. Any errors are attributed solely to the author, with appreciation extended to the supporting contributors.
Auteur
Matthew McCulloch
Responsable de la décarbonation chez Norda Stelo