.jpg?width=432&height=228&name=heroBlog%20(1).jpg)
News and blog posts
Collective Ingenuity
Filters
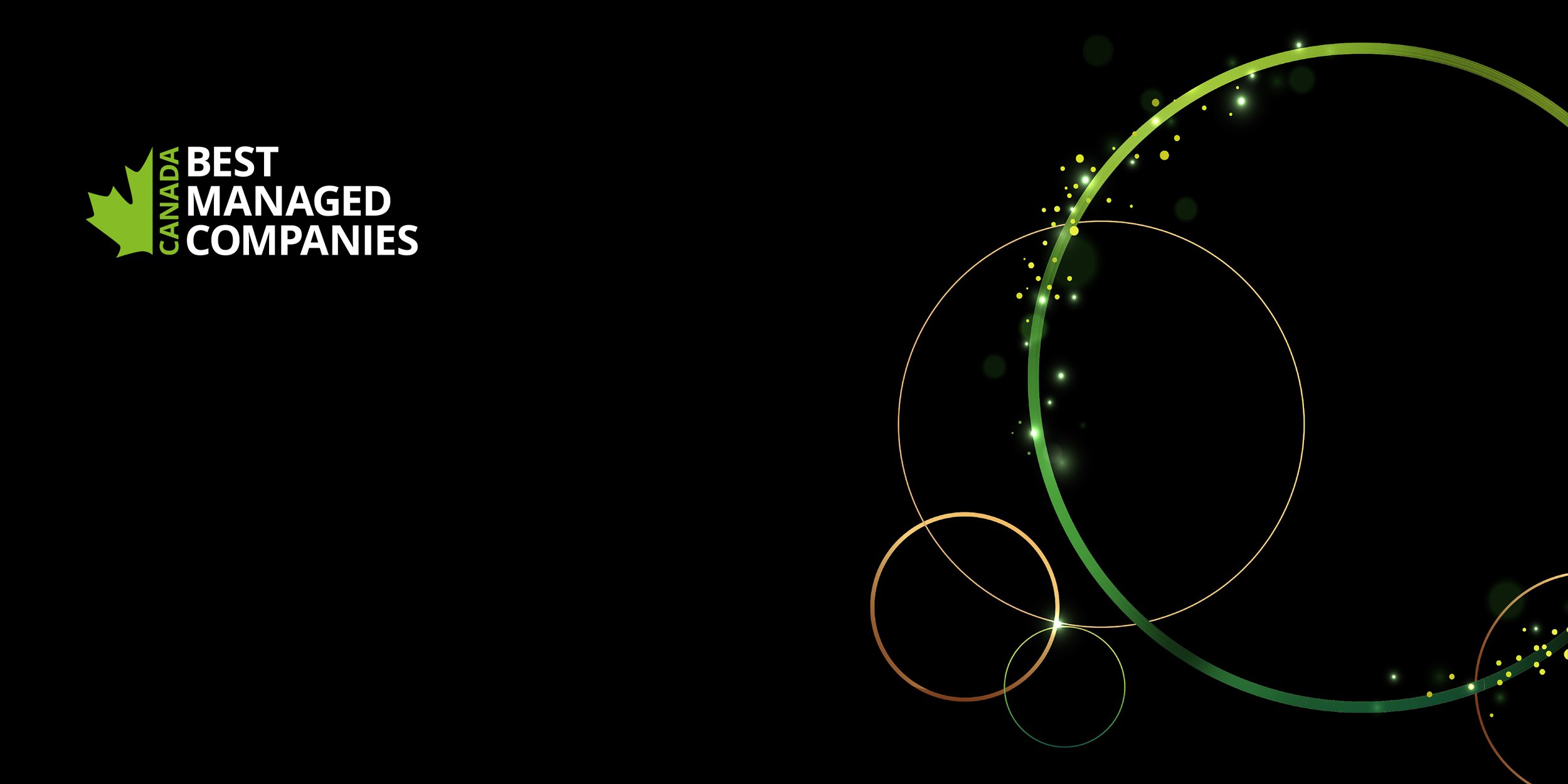
Norda Stelo Named Gold Standard New Winner of the Canada’s Best Managed Companies Program
Norda Stelo was recognized for its industry-leading performance, its global business practices, and its sustained growth by receiving the prestigious 2025 Canada’s Best Managed Companies award. Norda Stelo won its initial Best Managed award in 2021 and has successfully retained its status, becoming a Gold Standard winner in 2025.
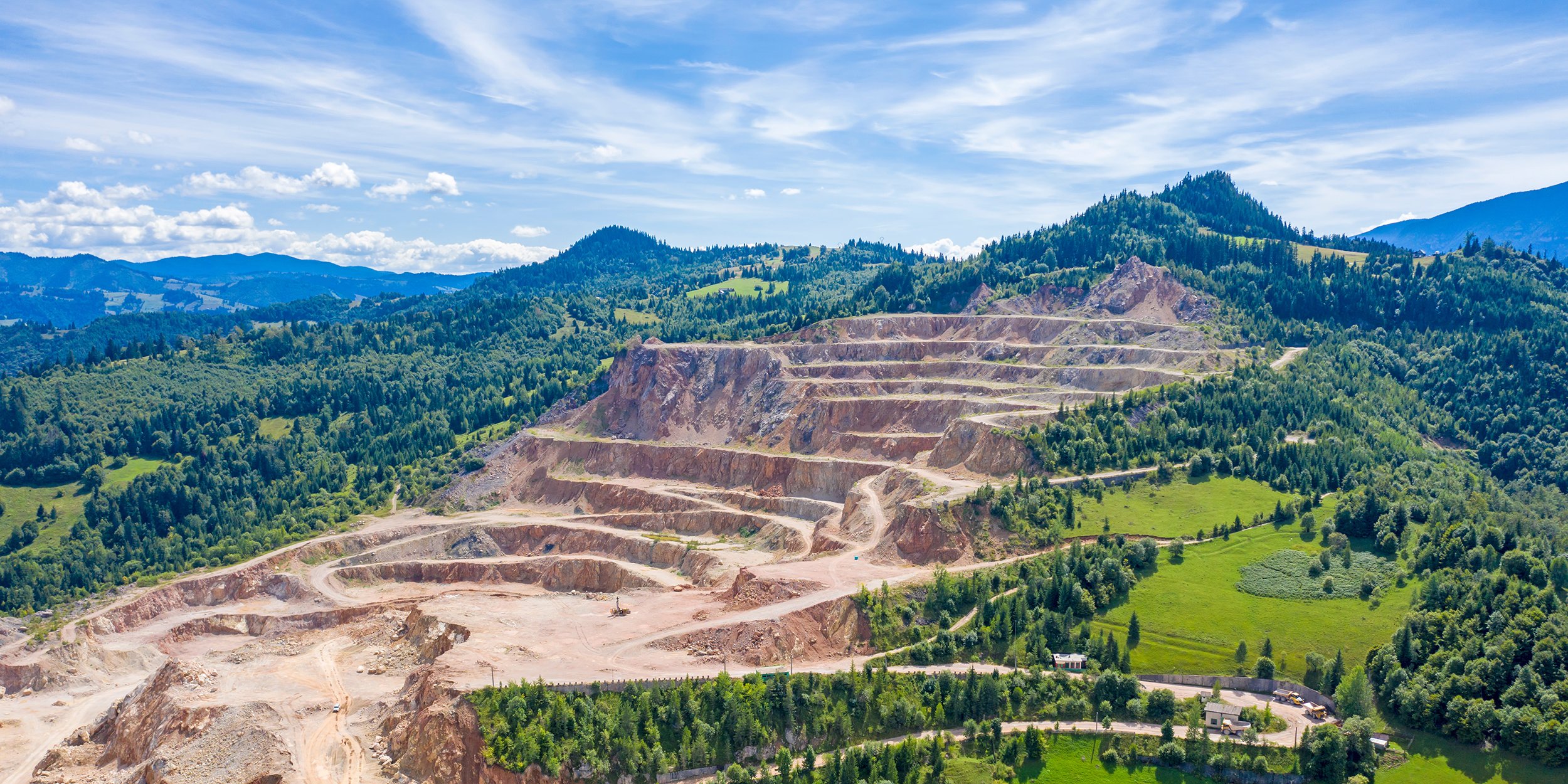
Environmental Impact Studies: Main Considerations for Sustainable Mining Practices
In a context where social and environmental acceptability has become a crucial issue for mining projects, environmental impact studies (EIS) are emerging as an indispensable strategic tool. Far from being an administrative formality, the EIS is at the heart of best practices in environmental risk management and serves as an essential lever to guide mining development toward greater sustainability.
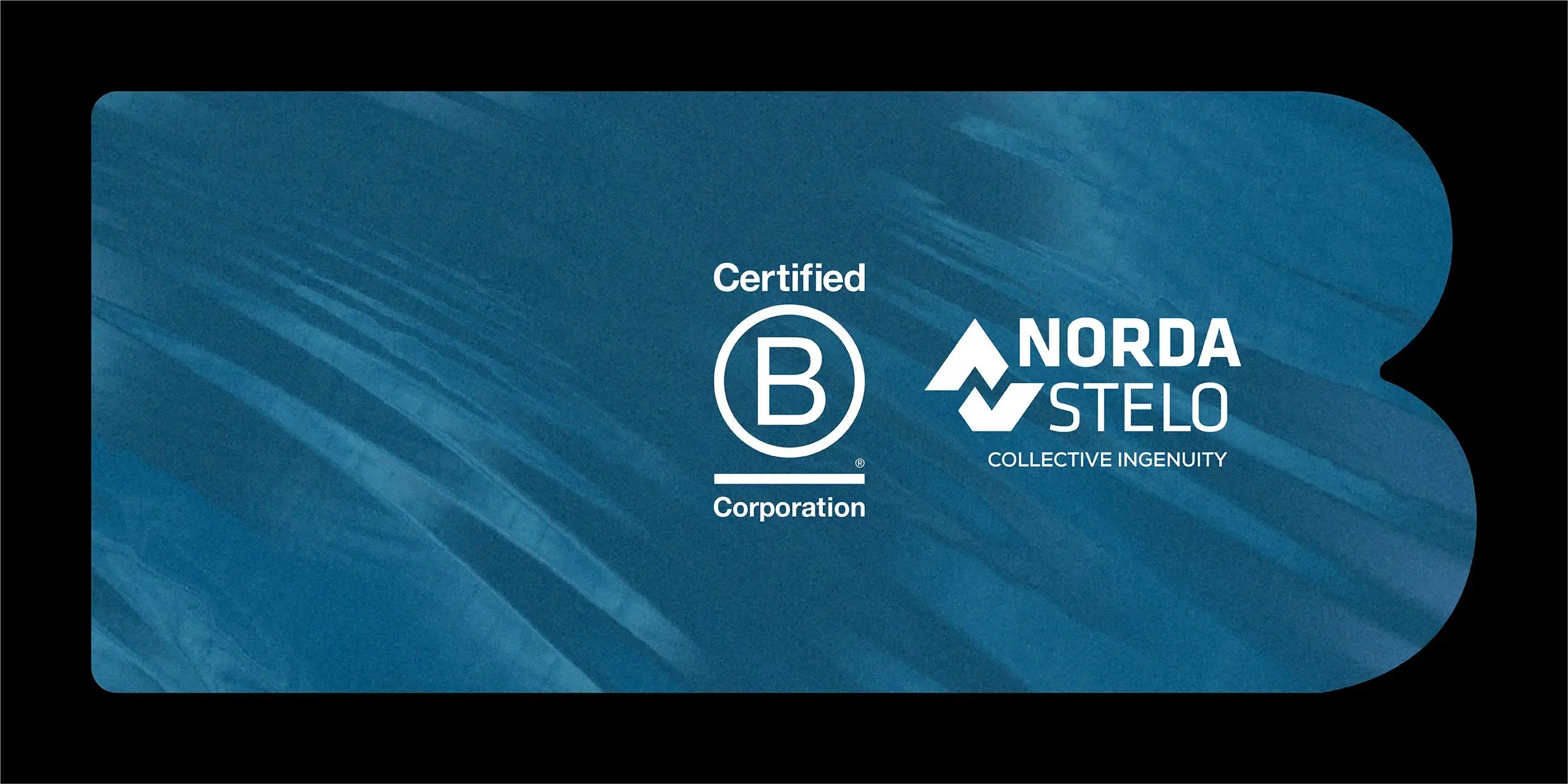
The 5 Key Benefits of Choosing a Certified B Corp
As climate pressures intensify and scientific experts increasingly call for action, the way businesses operate is also undergoing a major transformation.
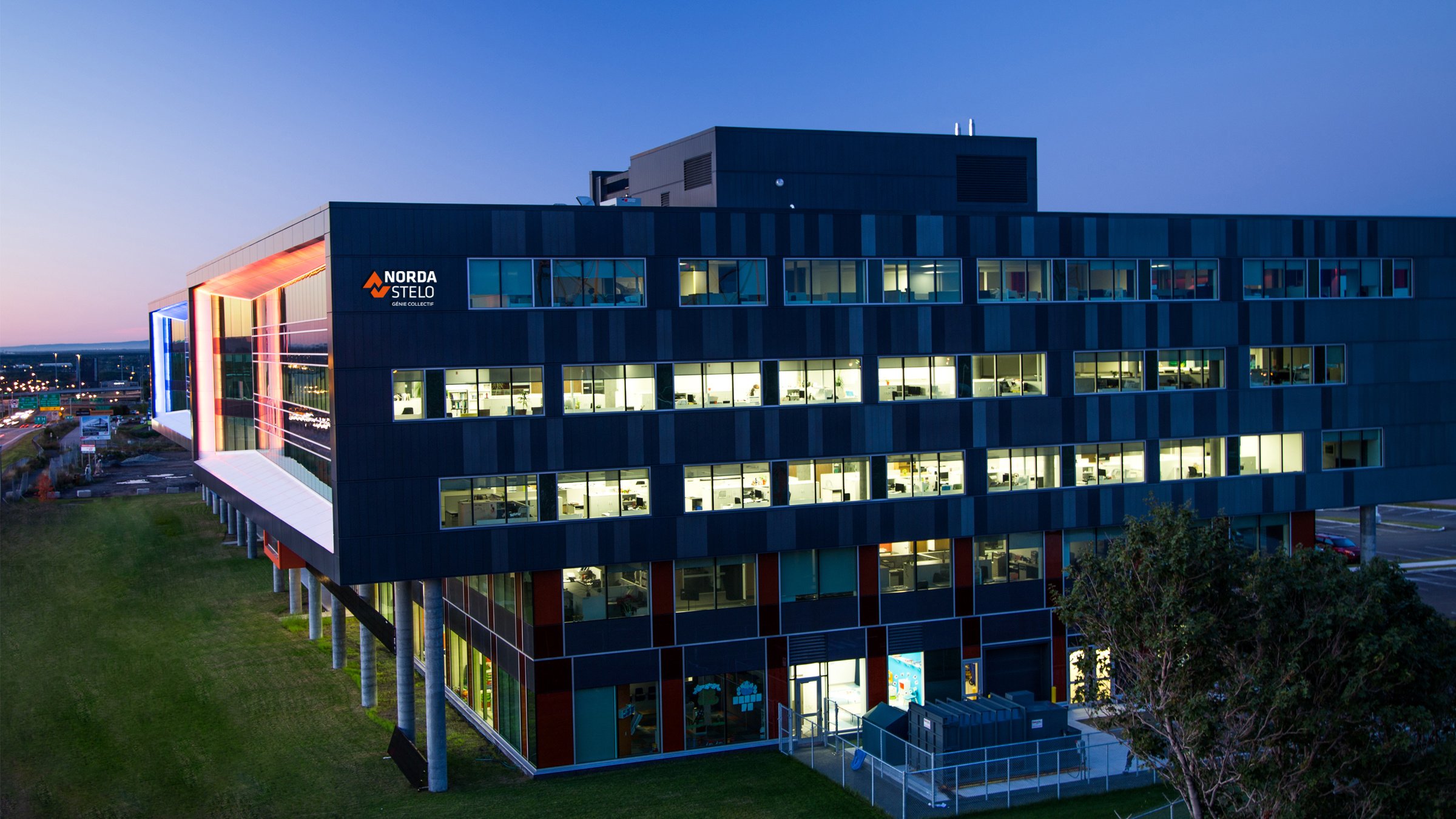
CDPQ becomes a shareholder of Norda Stelo: A partnership to accelerate sustainable innovation
Norda Stelo is proud to formalize CDPQ’s capital stake after two years as a lender. This strategic partnership is aligned with a shared vision of innovation, sustainability and global outreach, marking a key move for Norda Stelo, Québec leader in impact engineering.
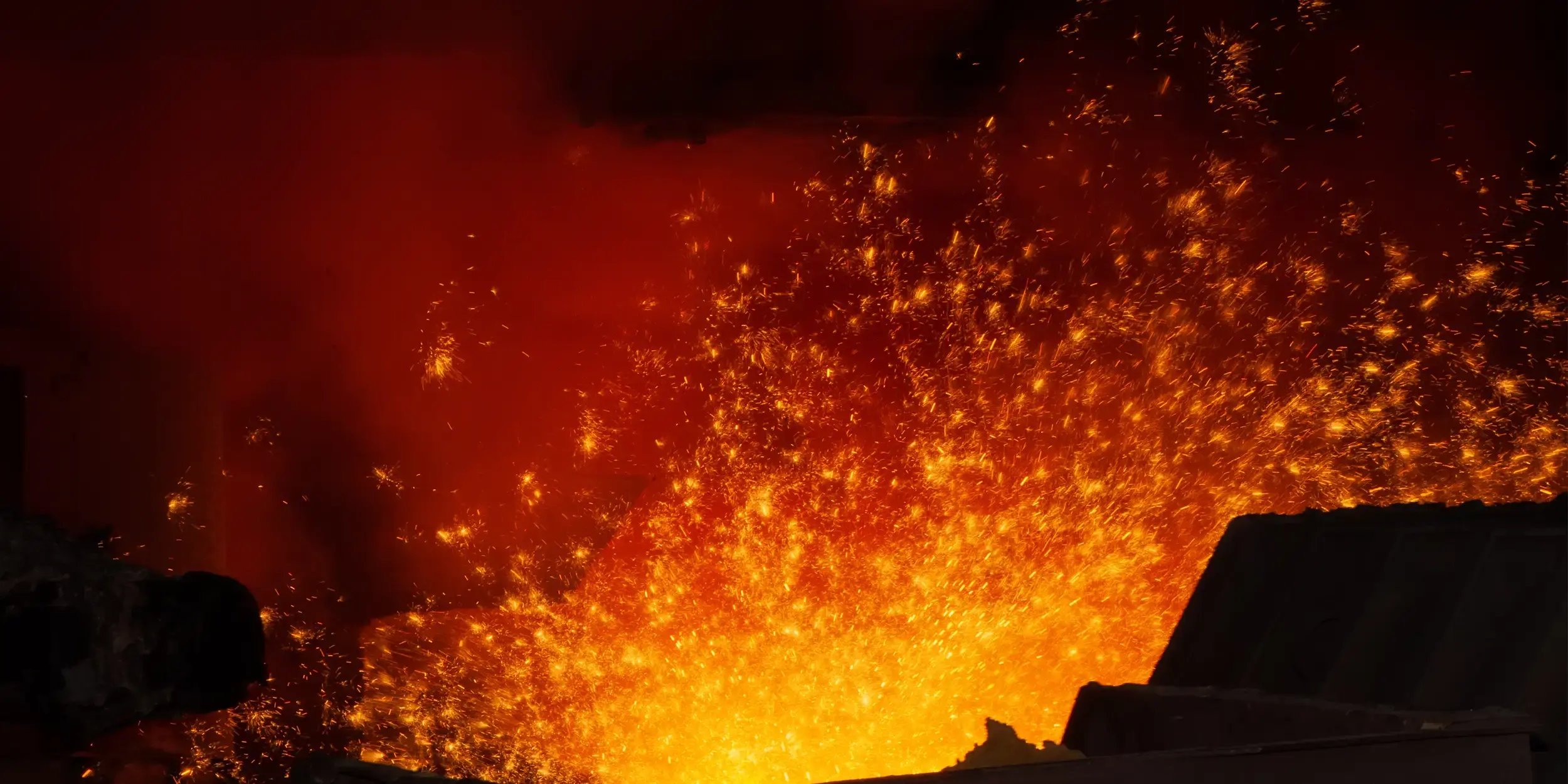
High Temperature Process Equipment Decarbonization
In the collective effort to decarbonize our industries, certain sectors face greater challenges in this endeavor. Such “hard-to-abate” sectors are industries characterized by process-related carbon emissions and other hazardous air pollutants, with limited straightforward options for significant emission reductions.
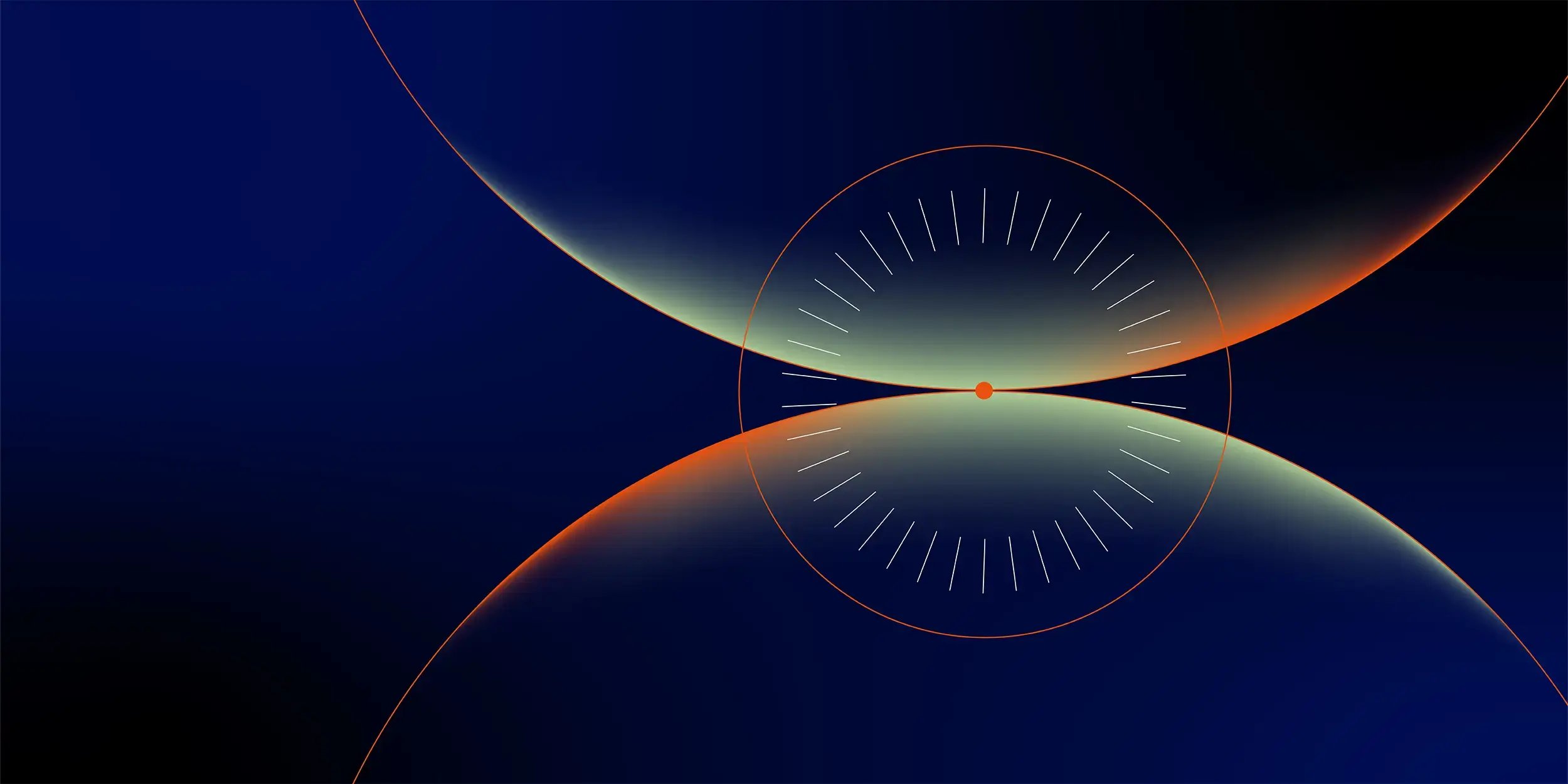
Norda Stelo presents its new vision of engineering
Norda Stelo marks an important milestone in the evolution of its business strategy by affirming its role as a leader in impact engineering.