
Key Elements in the Design of Efficient Soft-Transfer Materials Handling Systems for Reduced Dust Generation
Dust control has become an increasingly important health, safety, and environmental concern. This is particularly important at ports and terminals handling dry bulk materials because of their proximity to the water and, often, neighboring urban communities.
Active Dust Control versus Passive Dust Management Methods
Active dust control methods are used to suppress or collect fugitive dust generated by material handling processes and conveyance. These methods include equipment such as dust sprays, fogging and chemical systems, wind fences, baghouses, cyclones, and wet scrubbers. These active methods can be highly effective in reducing fugitive dust emissions that have already occurred.
However, preventing or minimizing the occurrence of fugitive dust from the outset, by employing effective passive dust-management methods in the early design phases of bulk materials handling systems, can diminish the need for active dust control.
Initial Considerations: Materials Analysis and Design Techniques
Discrete Element Method (DEM) modelling is a technique used to simulate the movement and effect of numerous, small, solid particles such as those found in bulk materials handling industries. These particles can be anything from coal and potash to rocks or wood fiber, in essence, any solid material made up of particles.
Computational Fluid Dynamics (CFD) modelling uses numeric analysis and data structures to solve problems involving fluid and air flows, simulating their movement around objects.
A reduction of dust emissions can be achieved in the early design stages through careful analysis of the materials’ properties and the use of design techniques such as DEM or coupled CFD-DEM model analysis to produce soft transfers of dry bulk materials. This proactive design approach reduces the need for costly active dust control methods and results in a more efficient throughput, while minimizing product degradation, clean-up requirements, and waste.
Description: The images below depict how coupled CFD-DEM simulations are used to validate and optimize the transfer design to reduce dust generation. The image on the left depicts an existing transfer which had issues with fugitive dust that was modelled to validate the simulation. The image on the right depicts the re-designed transfer which has been optimized to reduce dust generation.
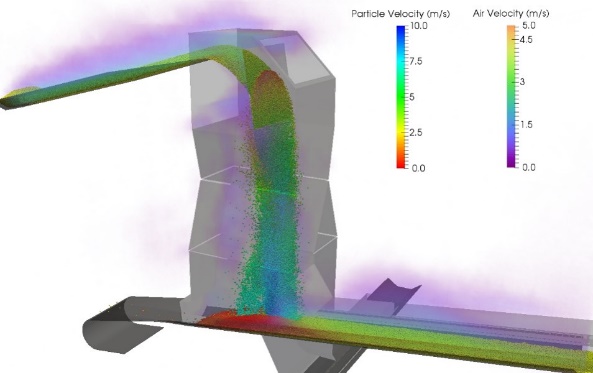
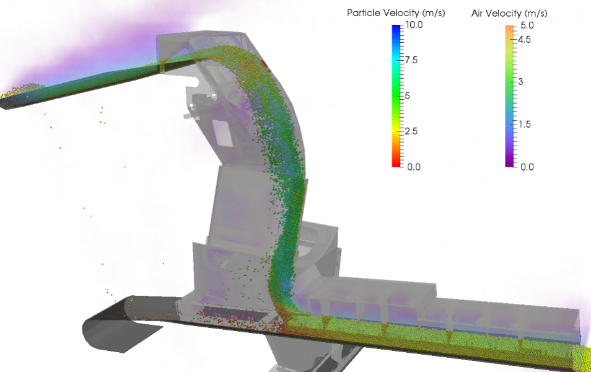
Modern design tools, when combined with expertise and proven validation techniques, can be used to develop conveyor chute designs which control the material velocity in a manner that minimizes dust generation. This is ideally achieved by keeping dusty materials in constant contact with three-sides of the chute and varying the angle and cross-section of the chute to maintain a constant material cross-sectional area.
For new conveyor designs, it is critical to consider the optimization of material transfers at the beginning of the design process to ensure the conveyors are laid out in a manner that allows for the most efficient configuration. This helps avoid the need to modify the conveyor geometry at later stages of the design process when it would be relatively more expensive and time consuming. However, all too often on projects the transfers are not given satisfactory attention during the design phase. This can be much more costly in the long run due to the expense of additional operations and maintenance measures required to address fugitive dust emissions, product degradation, clean-up, and waste that results from an inefficient design. Additionally, retrofit modifications will be relatively more expensive compared to what it would have cost to optimize the design in the first place.
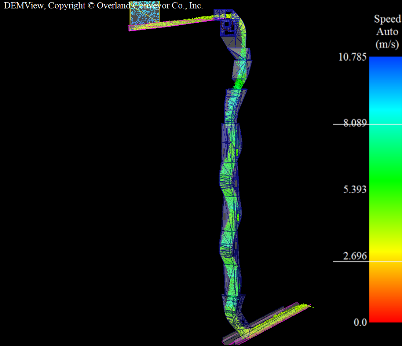
Description: A relatively tall transfer designed to keep material in near constant contact with three sides of the chute and within a tight velocity range.
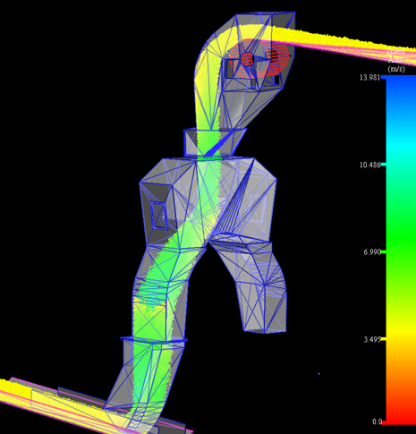
Description: A 1 to 2 transfer designed to turn the material in the direction of the receiving conveyor with minimal deceleration at the impact points in order to reduce product degradation and dust generation.
Key Design Elements
The Key Design Elements to be considered during the early design stages of a dry bulk material handling system include:
- Evaluation of Material Properties
The design of bulk material handling systems begins with understanding the material. Determine the key properties of the material to be handled (such as material density, wall friction angles, and particle size) by sending materials to a test laboratory for analysis. - Conveyor Speed Selection
Choosing the appropriate conveyor belt speed will reduce the likelihood of product spillage and dust generation. - Determination of Vertical Incline
Ensure that the conveyors’ vertical inclines are appropriately sized for the material in order to avoid roll back. - DEM Modelling to Validate Chutework Design — Simulation Input
Observe and model an existing transfer to acquire real-world input for DEM or coupled DEM-CFD simulations to help ensure that the model accurately simulates the real-world flow of materials. - Soft Transfer Systems
Soft transfer systems can be achieved through DEM or coupled DEM-CFD modelling analysis, used to optimize material flow and trajectories in chutes including the influence of moving surfaces to reduce turbulence in the material flow, thus minimizing dust emissions, product degradation, and waste. Key components of the analysis include:- Optimized drop height.
- Optimized position of the discharge pulley relative to the receiving conveyor.
- Minimizing the size of open areas to reduce induced air.
- Design of the loading zone so that dust-laden air is slowed down to give the dust an opportunity to fall back onto the belt.
- Reduced impact angles.
- Design of the material flowing through the chute in a tight cohesive stream to prevent dust from escaping.
- Ensuring that material is centrally loaded onto the receiving conveyor.
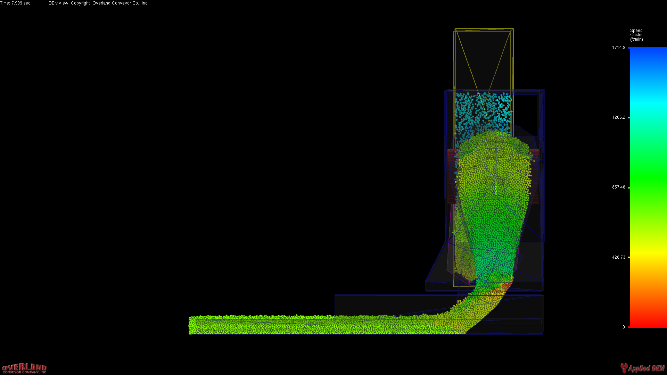
Description: A relatively short transfer designed to keep the material in a tight stream and in contact with 3 sides of the chute to reduce dust generation.
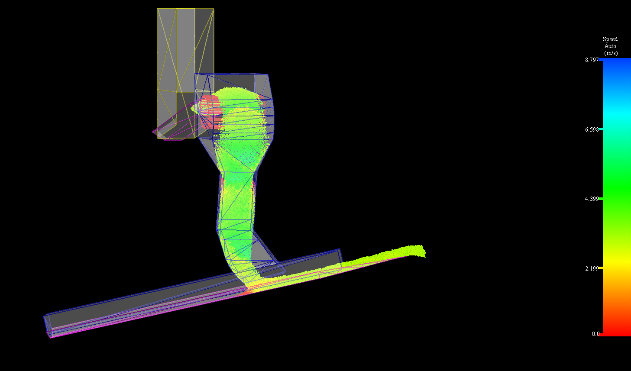
Description: An existing intermediate transfer with less-than-optimal discharge and receiving conveyor geometry which was re-designed to optimize performance.
Attention to these key design elements during the early design phases of material handling systems will optimize the material flow and reduce dust generation, resulting in a safer work environment, the reduction of emissions, and an improved throughput. Additionally, remedial system modifications and the need for active dust control methods can be reduced, resulting in significant cost savings.
Tags In
Leave a Reply Cancel reply
Found this article interesting? You will certainly like...


